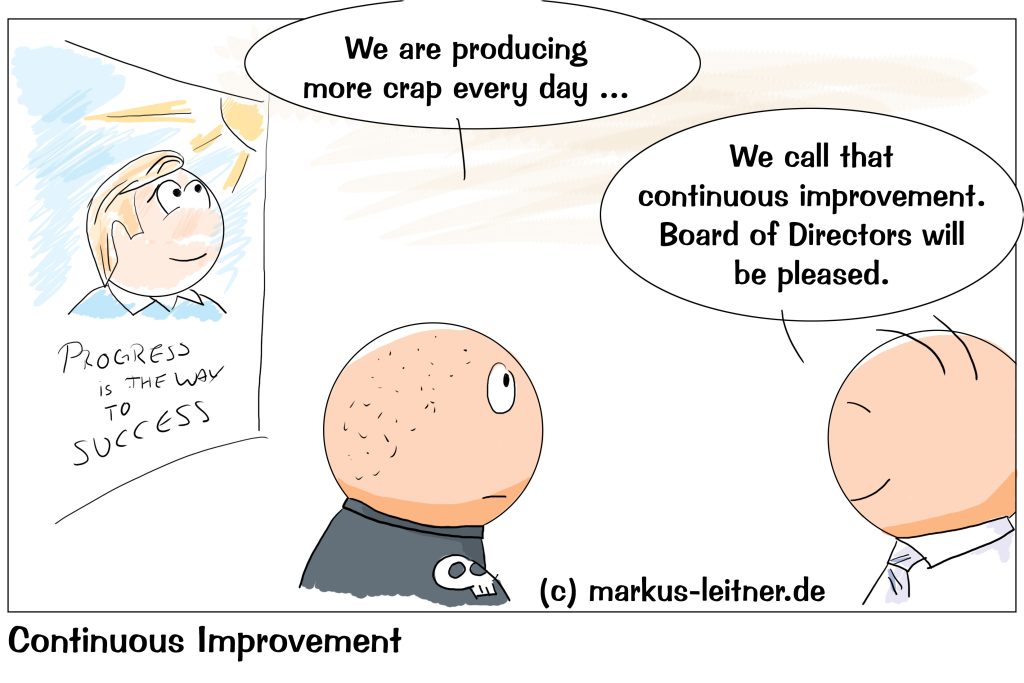
If someone mentions »Kaizen« our bullshit-bingo-alarm rings. We hear about that in every agility training and every second management seminar. Unfortunately we only hear one or two sentences that do not really explain anything, and how to do that I real life is not told anywhere.
With the paraphrase »continuous improvement process«, the explanation is ticked off in most cases. Not only that many people have little idea of what that means, there are also many different opinions of what it could mean. The simplest of them would be: we regularly do retrospectives – topic ticked off.
Hopefully it will not surprise you that this does not go far enough.
Kaizen is a much more holistic approach that encompasses the entire organization, but it is generally used to refer to a single team – so we are only looking at a small part of the whole. When we strive for »continuous improvement«, it does not help if we only look at a tiny part, after all we all know that every team has an infinite number of interfaces to the outside world. So how are we going to achieve lasting change if we ignore everything that is happening around us?
I am not going to start with the history of Kaizen and Agility and Toyota and all that crap, we just have to understand and accept that an improvement process has to work at all levels of the organization involving all employees and managers. This includes quality management, suggestion schemes, further training, processes and so on. Everything you can think of that involves changes in the organization is ultimately part of it, and that brings us to our biggest problem: it quickly becomes very complicated and complex because we have to consider an almost infinite number of aspects.
But more on that later when we go into practice…
First, a bit more theory: Kaizen has some basic principles. In a way it is quite similar to Kanban, where we also just find some principles that we have to bring to life ourselves. How we want to do that is up to us. Luckily, there are already some things that have proven themselves in a number of companies that we can fall back on.
Process vs Product. We have the choice to make constant improvements to our product or constant improvements to our processes. Kaizen says that it makes sense to focus on the processes because that way we will find things that translate into product improvements, e.g. in working with our customers and users. If we get better at it, it should automatically affect our product. And because we have improved the process, this product improvement is automatically perpetuated. Here, too, a holistic view that takes into account connections, causes and effects.
Customer focus. We should already be familiar with it from agility, but Kaizen is quite pragmatic there. Satisfied customers pay for our services, and retaining customers is easier than acquiring new customers. After all, we do not do all that nonsense because we are such good people, we want to make money with it. We manage this quite easily when our customers buy updates or order the next model. So, it is in our interest to see and understand the customer’s point of view.
Quality orientation goes hand in hand with customer orientation and can therefore even be understood as a partial aspect of it. Of course, users will be happier with a higher quality product. In Kaizen, however, we have a very central question here: how do we constantly increase the quality of our products? This is where terms like total quality management come into play, metrics, measurement methods and quality standards. This is nothing new in manufacturing.
Another principle of Kaizen is that criticism and suggestions are a constant opportunity for development and thus for improvement. So, we are encouraged to think about a culture of feedback to keep adding new aspects to our thinking and efforts. It should also help us to really involve all corners of the company.
Finally, all changes that have a positive effect are converted into standards in order to permanently anchor them in the organization. This last point is very important, because this is the only way we can achieve sustainability and a steady approach.
When we start thinking about how to put all of this into practice, we can look at two things: the small and the big. The small approach is what you all probably know – working in a team.
The retrospective is only part of our work. Continuous improvement can happen every day. In our retros we pay particular attention to two things: many small steps also bring us forward, and a change only helps us if it is also sustainable. We are not always looking for the one big hit – you have probably known that for a long time. Above all, our retrospectives build on each other. What did we discuss last time? What has become of it? Which step should now follow? We want to avoid starting all over again, otherwise our retros will remain piecemeal and we will not achieve continuous change.
We achieve this relatively easily by not only creating and tracking the actionables of our retrospectives as items in the sprint, but also picking them up again in the next retrospective, analyzing the change achieved and discussing the next steps. So we work on big topics in our teams iteratively. We do not necessarily need our own backlog for this. One page in your Confluence is completely sufficient, where we list the topics we care about and then always continue with action / effect / next action etc. At some point we will decide that we can check off an issue because we think it is on a good footing. That is perfectly fine, even if it would go against the pure kaizen idea, but we also need to see which areas require more attention than others. Therefore, it is also perfectly fine to ask with each retro whether we want to continue on that particular topic or tackle another that is causing us more pain.
The great Kaizen approach cannot be done without allies. If we know that we actually have to look at all parts of the company, we cannot avoid getting the support of management. If we can’t get to that, we go to the largest scaling that we can achieve.
Then it gets complicated because we have to explain to these people what we want to achieve and what it all entails. My advice on this is: do not play bullshit bingo. Make the terminology understandable and put yourself in the position of your listener. What are his (or her) interests? What should motivate this person to make a great effort with you? We want to achieve constant further development of the organization, but not for its own sake, but because we want to save effort, reduce waste, optimize processes, etc. In the end, there is a better product, faster on the market and cheaper to produce. Just as agility is not an end in itself, Kaizen is not an end in itself. At the end of the day, it is all about economic considerations.
Once we have the support of the maximum scaled level we can reach, we start gathering the aspects that we think are relevant. Here we are, for example, with the processes, for which we naturally need the process managers. We are on quality management and training programs and possibly much more. This means that we must also win over all of these people who are responsible here for us and our considerations. What does the organization want to achieve and why? When we have communicated that, we discuss what that means in the individual areas and what measures result from it. All those responsible for these areas also inherit the responsibility for the Kaizen process in this area at the same moment. We cannot and do not want to control everything centrally, but we should encourage regular exchange. What is happening where? What works and what does not work so well? How can we support each other across departmental boundaries? This exchange should also serve to coordinate things as far as necessary and reasonable.
In daily work, for example, Ishikawa and the three Mu (Muda, Mura and Muri – waste, deviation in the processes and overload) are quite good approaches, but these are only for analysis. Developing our measures is a completely different matter. Here we are at suggestions, experiments and evaluations.
Core: Kaizen is more than just the simple principle of continuous improvement. The overall organization is a holistic approach that encompasses all aspects of the company. If we want to make a difference here, we need the support of everyone involved.
If you need any assistance or want to know more, just speak to me.